Hose Assemblies
DIN 2817 Safety Clamps
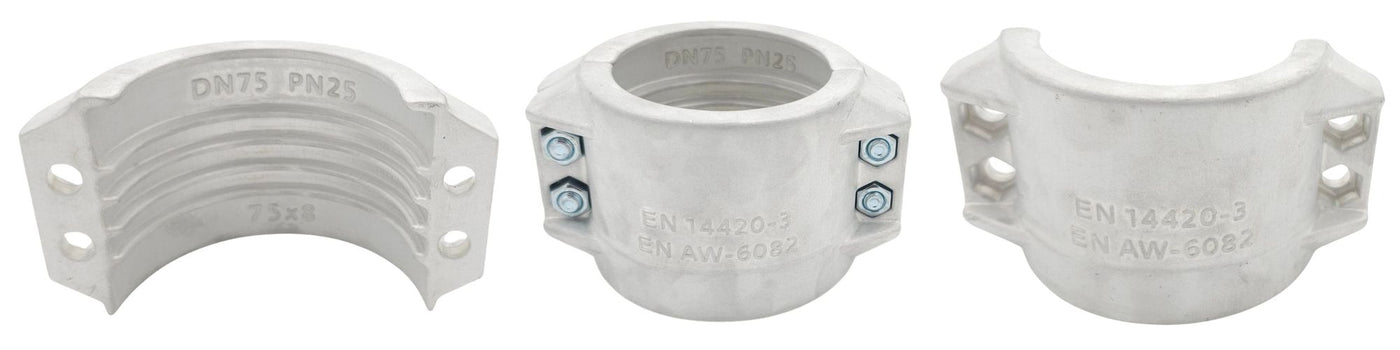
Once the pair of DIN 2817 Safety clamps are secured to your Hose & Coupling they are no doubt one of the strongest connections. Commonly used in many hose assemblies. Simple to fit, make sure you have the correct size pair of clamps for your hose, secure all 4 nuts / bolts and away you go!
T Bolt Hose Clamps
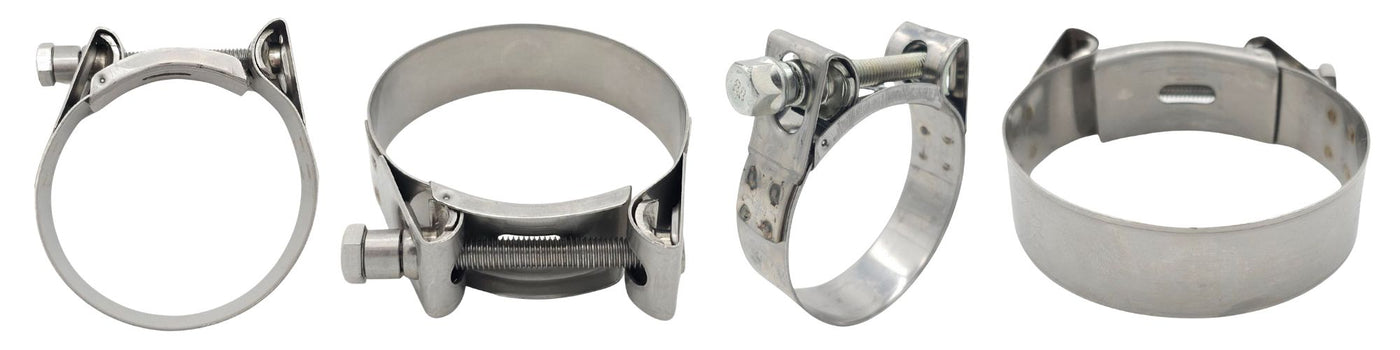
Preformed Clamps
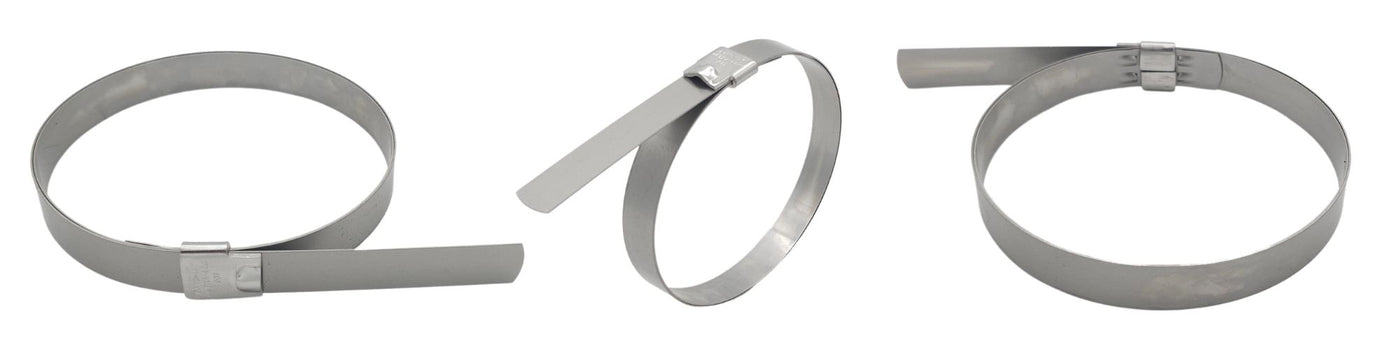
Designed for quick installation, highest clamping force and gap-free inside diameter. The best choice for demanding applications!
- Strongest band clamping system available.
- Double wrapped 201SS for superior strength.
- Unique lock formed under full tension maximizes tightness.
- Smooth inside diameter designed to eliminate leak paths.
- Buckle hood protects lock from snags.
Swaging
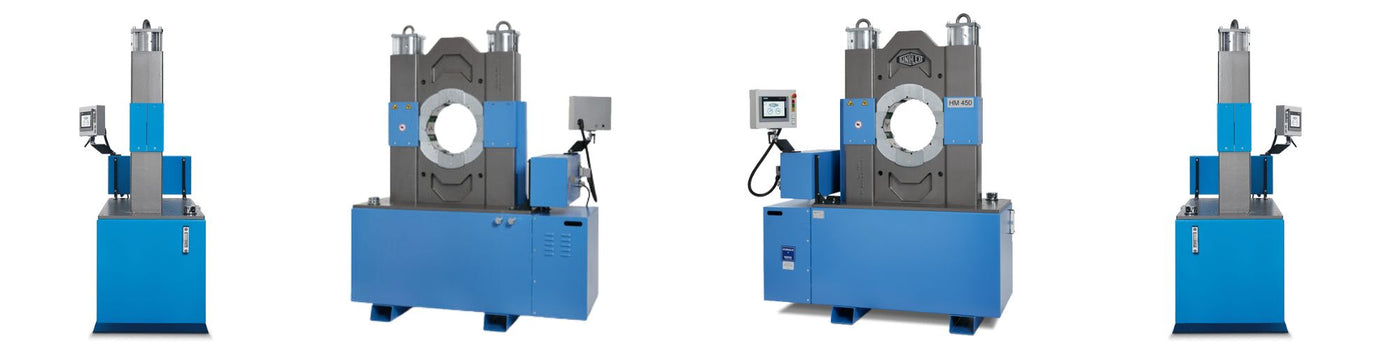
The primary function of a hose swage machine is to compress the hose and fitting together using high pressure and force, resulting in a tight and permanent connection. The machine typically consists of a hydraulic or mechanical press, a set of dies, and controls to operate the machine.
Here's a general overview of the hose swaging process using a hose swage machine:
- Preparation: The hose is measured and cut to the required length. The ends of the hose are usually cleaned and inspected to ensure they are free from dirt, debris, or damage.
- Selecting the appropriate dies: The correct dies for the specific hose and fitting size are chosen. Dies are typically interchangeable and are selected based on the diameter and type of hose being used.
- Positioning the hose and fitting: The hose end is inserted into the fitting, ensuring that it is positioned correctly and fully inserted.
- Operating the machine: The hose and fitting assembly is placed into the hose swage machine, with the selected dies positioned accordingly. The machine is activated, applying pressure to the dies and compressing the fitting onto the hose. This process is usually hydraulic or mechanically powered.
- Checking the crimp: Once the crimping process is complete, the crimped assembly is carefully inspected to ensure it meets the required specifications and standards. This includes checking for proper alignment, tightness, and any signs of leakage or defects.
Fill in the form below to get in touch
Subscribe to our emails
Be the first to know about new collections and exclusive offers.